Our Manufacturing Execution System (MES) corresponds to the navigation system in your car
Would you ever drive without your navigation system? Our MES is doing the same job for your production as the navigation system is doing for your driving.
- It tells you the estimated finishing date for every order
- It gives you clear instructions on what to do next
- It automatically reacts to deviations by re-calculating a new "route"
Employees have to stick to the plan or document deviations. The production steps are documented including measurement results. In this way you can proof the quality of the production to your customers. Therefore we fulfill all the requirements of an MES according to the VDI-standard 5600
Our MES helps you in the following aspects
- Create transparency by means of meaningful reports and overviews
- Reduce the effort to collect data by an intuitive user interface
- Improve the logistical KPIs as delivery reliability, capacity utilisation, inventory etc. by an optimized plan
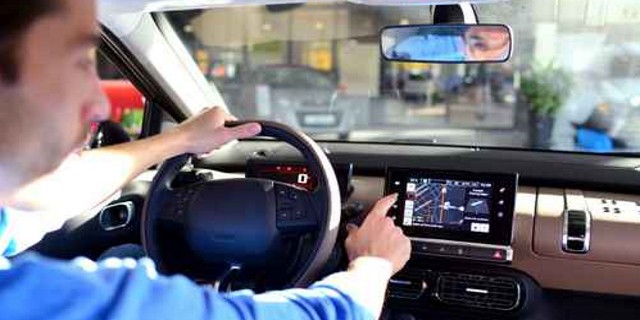
Advanced planning and scheduling (APS)
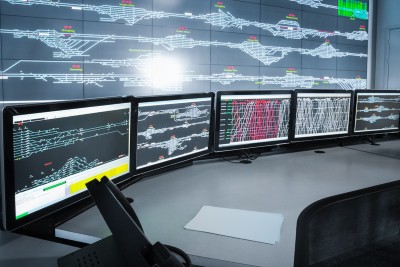
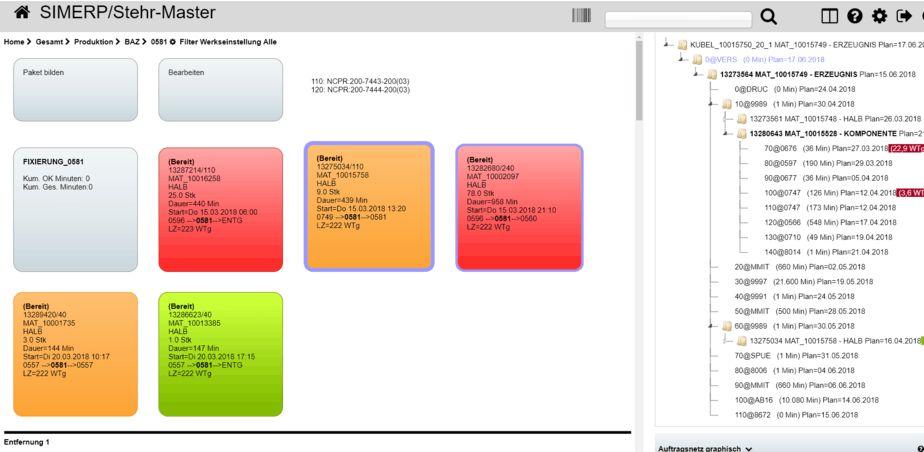
At the core of our system is the planning algorithm for your production. Here we determine the optimal sequence and machine/personell assignment. Of course we optimize the material reservations in multiple disposition levels as well as the assignment of employees to machines by means of a qualification matrix.
Even in large production environments our system needs less than a minute for the calculation. This and our simulation environment allows you to evaluate different scenarios. The system shows a list of all the differences between the current plan and the newly created scenario.
The system optimises the capacities. However, often one can change the restrictions. Additional shifts and overtime can be planned, orders prioritized or purchase orders expediated. Such measures however have to be discussed by humans and requires their knowledge of people and processes. However, our system clearly indicates the problem areas and allows the team to evaluate a solution with a few clicks. Therefore we create transparency about problem cases.
One of our customers has improved its delivery performance from an already high level by another 10%-points. A typical factor was the user interface which is adopted for the typical questions needed in a production control department. Before our system the employees had to rely on SAP. However, due to the complexity of the analysis of a customer order took typically 10 minutes - now it is a matter of 30 seconds. Therefore now all orders can be checked regularly and in case of problems early changes are made. A second factor is the stability of the planning. A study of the research institute for rationalisation in Aachen shows compared our system to the previously used APS. In case of production deviations the old system has shifted orders 4-5 times more often than our system does. In this way our system offers much more reliable schedules.
Production data aquisition (PDA)
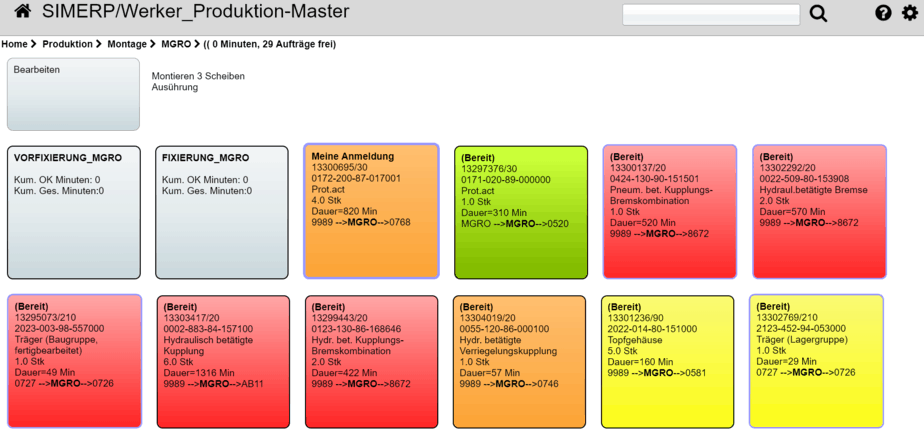
The plan of our APS module has to be executed. With many thousand operations and many deviations it is important to keep an overview. In our system one can grant or remove degrees of freedom from the employees. For every machine we can configure wether the worker has to stick to the order sequence or can optimize the schedule in a frozen zone. We even show orders with a similar setup.
The web-based system allows workers to use tablets, smartphones or industry PC to document problems on the spot. Of course they can also do the typical time, quantity, status and even location reporting. The last one reduces the time to find orders on the shopfloor. The results are displayed in an intuitive manner.
Worker guidance and quality module
Our integrated quality module is fully integrated in the PDA-solution. Therefore workers do not have to switch between different applications for a step-by-step guidance of their working instructions.
Unser integriertes Qualitätsmodul kann vollumfänglich in die BDE-Lösung eingebettet werden. Somit muss der Mitarbeiter nicht zwischen verschiedenen Anwendungen wechseln um eine Schritt-für-Schritt-Anleitung des Arbeitsprozesses zu bekommen.
Typically the work preparation creates a frame of working steps. This includes the tools and necessary measurements including their tolerances.
During the first production run this data can be modified and extended due to practical experiences. Employees can use the in-built camera of tablets and smartphones to take photos of setup, machine and tool or use a voice-input to collection additional hints.
When the same part is manufactured the second time all collected data can be displayed as step-by-step approach. No product can be confirmed without the required measurements.
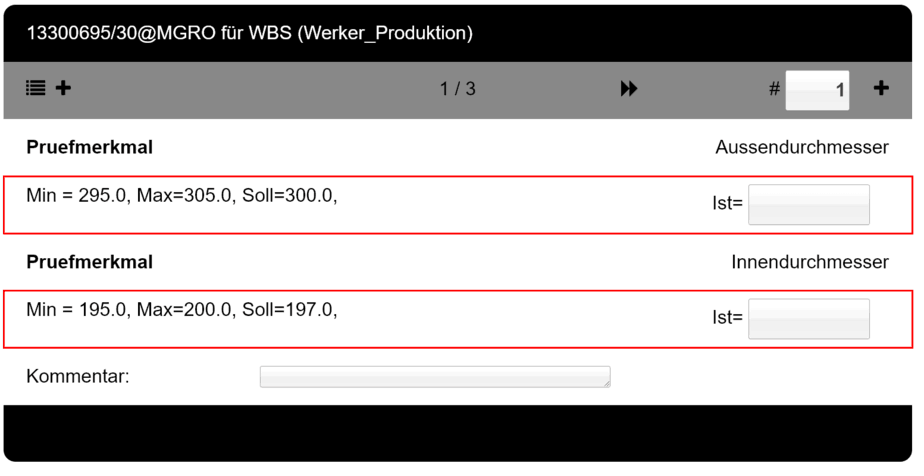
About us
Our company was created in 2016 in a consultancy project. We consider ourself as partner to manufacturing companies. We are not only selling software but help to achieve logistical objectives. Since ouf foundation we have regularly won prices as one of the best companies in the area of IT&software solutions for the industry. We are engaged in the society of the MES providers and at the RWTH Aachen in the cluster smart logistics where we cooperate on R&D. For us it is important ot fulfill your specific requirements and provide an easy-to-use system. We are happy to discuss your requirements with you.
Dabei ist uns besonders wichtig, flexibel Ihre individuellen Anforderungen umzusetzen und die Mitarbei-ter mit einem einfach zu bedienenden System zu be-geistern.
Gerne stehen wir für ein unverbindliches Beratungsgespräch zur Verfügung.
Convince yourself
Unser Imagefilm
Unsere Planungslogik
Industrie 4.0 mit SIM-ERP